Determination of a Load, Heat, Time-to-Failure Surface of Polymeric Composites
JA. Milke, AJ. Vizzini
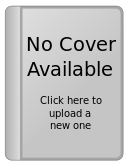
Published: 1993
Pages: 12
A small-scale experiment is developed to examine the failure of loaded composite structures exposed to a thermal insult for short durations. The test consists of imposing a tensile load of a prescribed magnitude to the specimen, then applying a moderate heat flux to a portion of one surface using a thermofoil micro heater clamped to the specimen. The heat flux is maintained for a period of 3 600 s or until failure of the specimen. A threedimensional failure envelope, with percent load, heat flux, and time-to-failure as the three axes, is determined for a given layup. In this study, 13-mm-thick test specimens were manufactured from a glass-fiber reinforced thermoplastic with the following layups: [902/0]11S, [0/(±60/0)11]S, and [0/(± 30/0)11]S. Over the range of loads and heat fluxes tested, initial failure locations occurred in the melted and unmelted regions of the specimens. The time-to-failure increases with decreasing flux for all laminates since the temperature gradients and damage level decreases. Differences in the time-to-failure for the three layups increase with decreasing heat flux or decreasing load. Thus, at low flux or load levels, the phenomenon is multidimensional; whereas at high flux or load levels, failure is one-dimensional, primarily dependent on the thickness of the specimen. As the ply angles comprising the laminate decrease, (that is, the laminate becomes more unidirectional), the time-to-failure increases for a given load and heat flux.